Manufacturing Tungsten Cemented Carbide
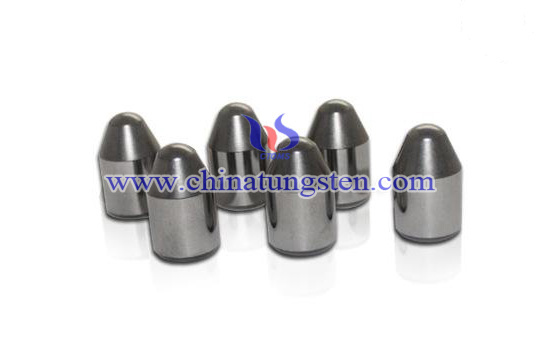
Tungsten cemented carbide is made by a powder metallurgy process. The compaction process is performed under very high pressure in a mechanical press as shown in Figure1 or in an isostatic chamber to form a part with the consistency of blackboard chalk. A small amount of wax (paraffin) is added to increase the green strength and help in handling the compacted shape. In this "green" state, it can be formed or shaped by conventional methods such as turning, milling, grinding, and drilling( Figure 2). The formed and shaped carbide is then sintered (placed in a vacuum furnace at a high temperature). During the sintering process, the carbide may shrink as much as 20% linearly, or nearly 48% by volume (Figure 3 and Figure 4).
For an "as-sintered" part, it is considered an industry standard to be able to hold a tolerance of ± 0.8% of the dimension or ± 0.005", whichever is greater. Tighter tolerances can be held on smaller pressed parts. After sintering, tungsten cemented carbide has achieved its full density and hardness. Tungsten cemented carbide can then be fabricated by diamond wheel grinding or electrical discharge machining (EDM) techniques.